let’s begin
I was very fortunate to be invited to the UK press launch of the new Ballantine’s Single Malt range up in Scotland, part of which was visiting the Glenburgie distillery.
What a treat.
This is a fabulously modern distillery which is not open to the public, only invited guests so this was indeed an honour.
In case you don’t know the backstory of the distillery, in the 1990s it was decided that the original Glenburgie distillery had had its day so instead of a refurb, the decision was taken to completely rebuild it on a green field site. The project was headed by industry legend Richard Clark, and as rebuilding distilleries is and was not the norm, he was given the rare opportunity to ask “what would you do to optimise production?”, and the results are incredible.
One of the most operationally efficient, with one of the most logical and easy-to-navigate layouts I’ve seen at a distillery, even the super-modern ones. This was not a retrofit, so they were able to design everything to be on one floor and the inclusion of automation at each stage ensured that the magic was not lost, but a recognition of what Chivas Brothers as distillers do well, and recreating that for the most precise distillation and spirit production possible.
To do this, Richard and his team spent six months observing and understanding how manual operations worked and what checks were performed so he could get to grips with how to recreate this in the new site. What he freely admits that he was not prepared for was the inert understanding the distillery ‘hands’ had for each part of the process. For example, they trucked in 21-day dried malt, which a machine can weigh and check to a degree, but what a machine cannot do is understand in a few seconds if the product was good enough to be used through rolling the malt in the hand to see if it crushes in the hand, tasting it to see its consistency for milling, check if it is hot or cold and to judge its latent moisture. Machines still cannot recreate these human processes, and the process is all the better for it. The job though is to understand these processes so that maximum control can be asserted onto each stage.
This was a rare chance to right all the wrongs from years of adding to and nuancing production, a chance to start a fresh
The distillery is designed so intricately that there is a sub-still wall under the distillery’s steel grated floor that is there just to prevent the warm air from the three wash stills and three spirit stills affecting the wash and the various other process data points that check that all is going well.
The new distillery is designed for a slim workforce, but it is still crucial that each operator knows about each piece of kit and what it is supposed to be doing all of the time so that when anything is not going according to plan they can step in and tweak or fix what is going on. Richard explains that it is “sort of like a kid on a bike and you let go… you set them free, but remain bloody close in case they have any issues”. That’s Glenburgie.
Quality control is key
Every week there is a spirit tasting by the blenders and distillers from each of the Chivas distilleries where a sample of that week’s new make spirit is tasted alongside a control sample to ensure consistency of output. Clark even notes that there was an instance where one week’s sample was deemed ‘better’ than the control but was rejected as it would not have been true tot he distillery character.
I love how Richard’s job is essentially to turn up to work each day and ask “is we understood that specific part of the process better, we could control it better… so how do we do that?”.
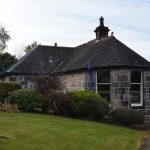
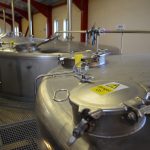
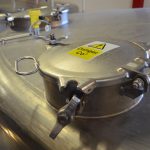
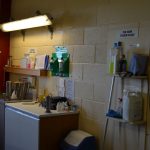
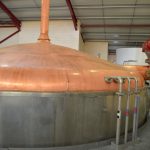
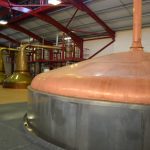
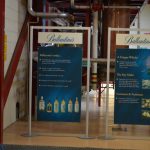
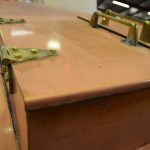
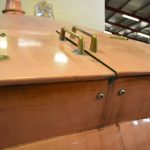
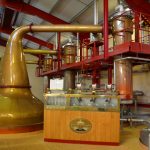
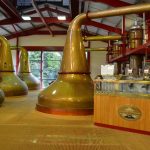
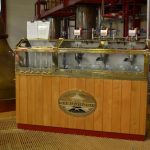
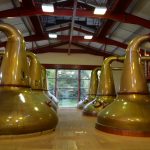
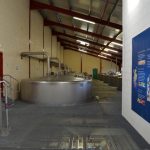
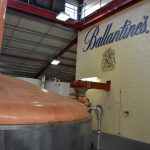
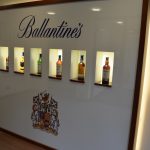
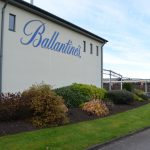
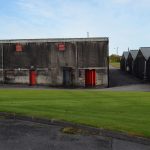
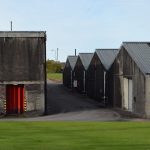
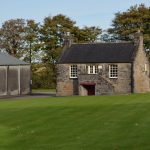
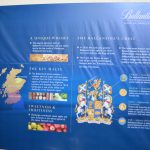